What Is Stop 6 Safety: Toyota’s Stop 6 Safety Initiative
Safety has always been a cornerstone of Toyota’s company culture, and it’s a legacy that dates back to the mid-20th century. From the early establishment of the Safety and Health Committee in 1938 to the stringent safety standards implemented over the years, Toyota has consistently prioritized the well-being of its employees. The commitment to safety culminated in the launch of the STOP 6 safety initiative in January 1992, which focuses on preventing the six most common types of workplace accidents.
So, stick to the post as I’ll explain everything about the STOP 6 safety initiative, its objectives, and the methods Toyota employs to ensure a safer workplace.
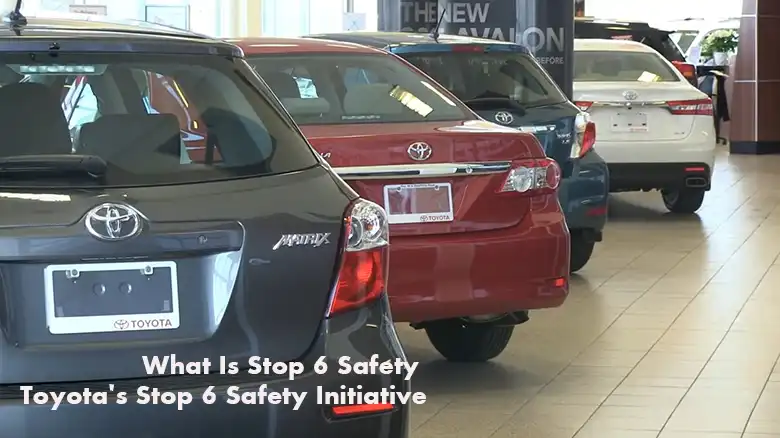
The Genesis of STOP 6 Safety
Toyota’s journey towards creating a safer work environment began with the concept of the Safety TOYOTA 0 (Zero Accident) Project. The project’s vision is to prevent accidents in six specific categories –
- Caught in or between machinery and equipment
- Struck by or against an object
- Falls from heights
- Electric shock
- Contact with hot objects
- Contact with harmful substances
This holistic approach embodies the belief that all accidents are preventable. The STOP 6 safety initiative was Toyota’s response to this belief and was designed to address the root causes of accidents to significantly reduce their frequency and severity.
Implementation of STOP 6 Safety
Toyota employs a multifaceted approach to implement STOP 6 safety –
Risk Assessments: Toyota regularly conducts risk assessments in its workplaces to identify potential hazards. Once identified, the company develops and enforces controls to mitigate these risks effectively.
Training: All Toyota employees receive comprehensive training on STOP 6 safety. The training covers critical topics such as hazard identification, risk assessment, and practical accident prevention measures.
Visual Management: Toyota utilizes visual management tools to monitor and display STOP 6 safety performance. This approach empowers employees to identify areas where improvement is necessary.
Continuous Improvement: Toyota is relentless in its pursuit of perfection. The company consistently seeks ways to enhance its STOP 6 safety program, including learning from accidents and implementing new controls to prevent similar incidents in the future.
Success of STOP 6 Safety
The success of STOP 6 safety is evident in the remarkable reduction of workplace accidents since its implementation in 1992. Toyota has achieved an impressive 80% decrease in the number of accidents at its workplaces.
Here is a glimpse of how STOP 6 safety is practically implemented at a Toyota workplace –
- Toyota installs guards and safety devices on all machinery and equipment, in addition to providing training on safe operation.
- Toyota maintains clean and organized workplaces to minimize tripping and slipping hazards, along with employee training on safe object handling.
- Toyota provides fall protection equipment and training for employees working at heights.
- Proper grounding and insulation of electrical wiring and equipment are strictly enforced, along with employee training on safe electrical work.
- Toyota marks hot surfaces with warning signs and ensures proper employee training on handling hot objects.
- Personal protective equipment (PPE), including gloves, goggles, and respirators, is provided, and employees receive training on safe handling of harmful substances.
Final Thought
Toyota’s STOP 6 safety initiative represents a comprehensive and dedicated approach to accident prevention. By focusing on the six most common types of workplace accidents, Toyota has not only reduced their number but also their severity, ensuring a safer and more secure work environment for its employees. This commitment to safety exemplifies Toyota’s unwavering dedication to its workforce and a brighter, accident-free future.